Worthing Road, Southwater
Horsham, West Sussex RH13 9YT
CONTRACT COMPLETION DATE Autumn of 2019
Dismantling Works – Former Production Unit & Service Area housed internally within Sony DADC Europe Limited’s Distribution & Warehousing Unit at Southwater Business Park, Worthing Road, Southwater, Horsham, West Sussex RH13 9YT
Sony DADC Europe Limited is a retail services provider of entertainment and consumer electronics, accessory brands and media. They are the leading end-to-end services provider for the entertainment industry and beyond, offering world-class digital and physical supply chain solutions and optical media replication services. The company’s network consists of service offices, optical media production and distribution centres worldwide.
Sony DADC proposed the dismantling and removal from their Southwater site of a redundant production unit and service area, housed within their large distribution and warehousing facilities main building. This provided an ideal opportunity for Dde to showcase a range of dismantling skills and demolition plant equipment and attachments during the summer of 2019.
The airtight production unit, demanding stricter standards for working conditions, consisted of pre-fabricated partitions forming the walls and ceilings encased in a steel portal frame of an area approximately 2,600m2 on plan. The service area was located on the mezzanine level, on a walk-on roof to the production unit, with a complex network of pipes, cabling and ducting, consisting of electrical services, water supply pipes, chilled water pipes, air extraction ducts, air pipes, material feed pipes, Argon pipes, vacuum pipes, and IT network.
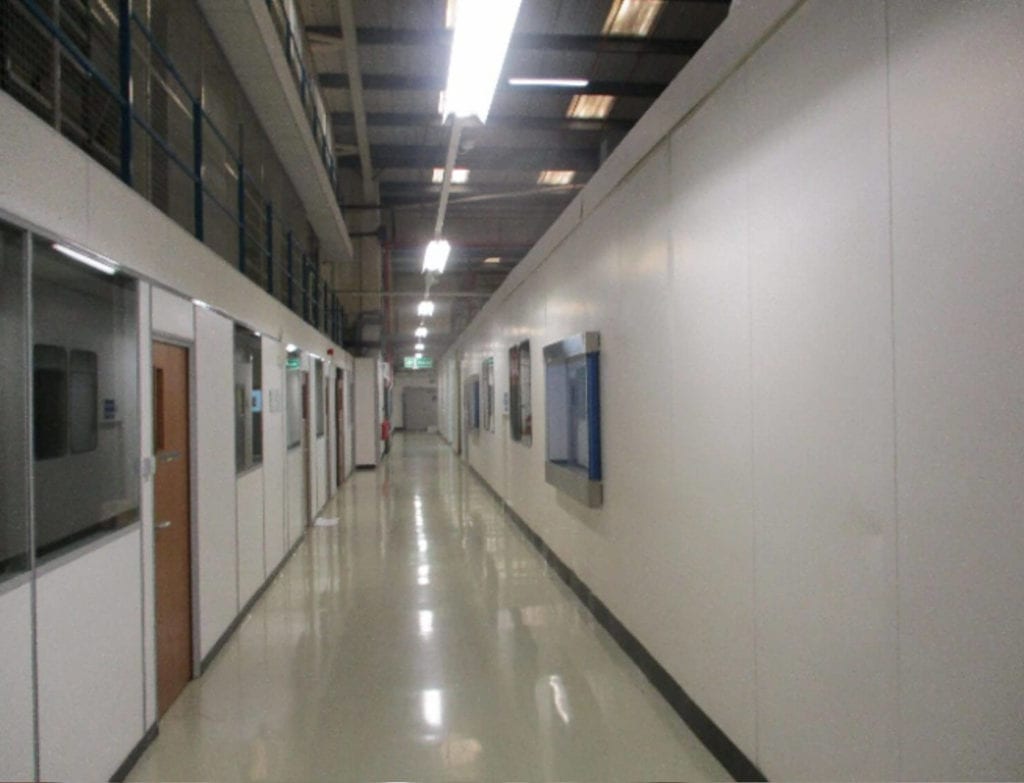
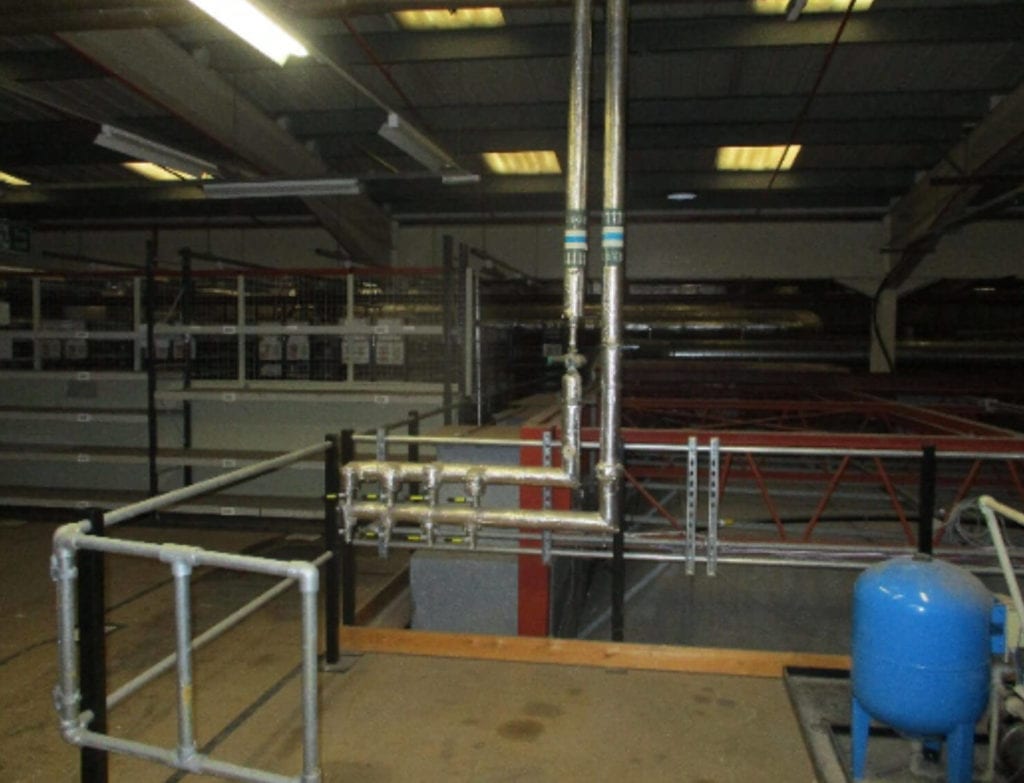
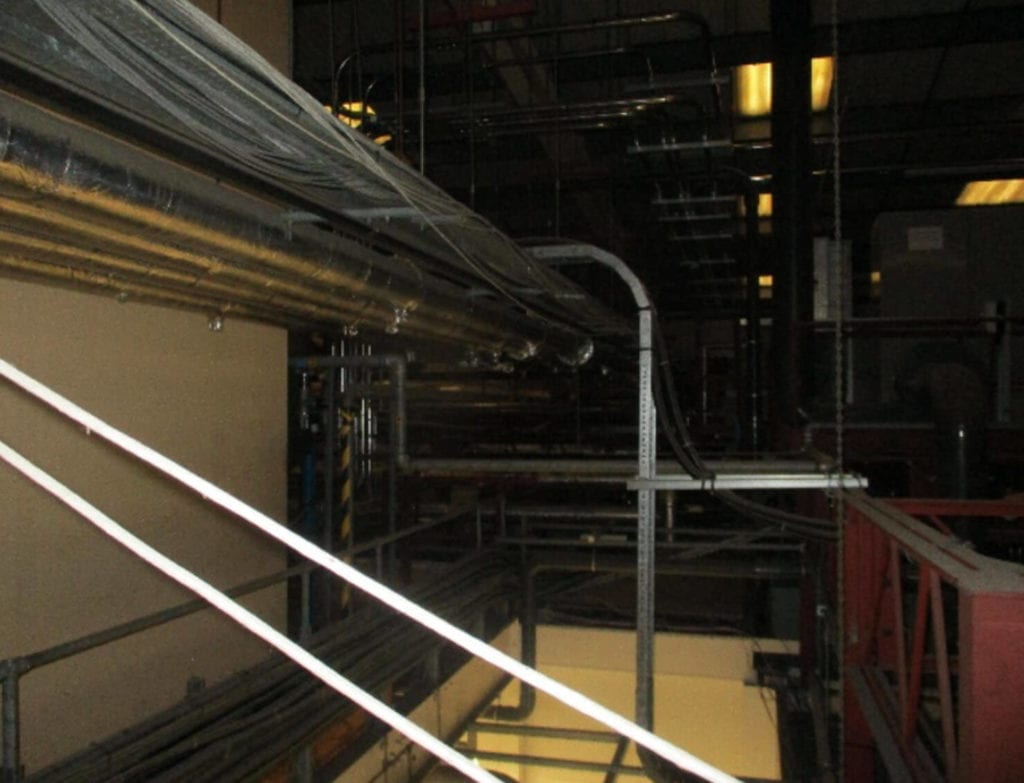
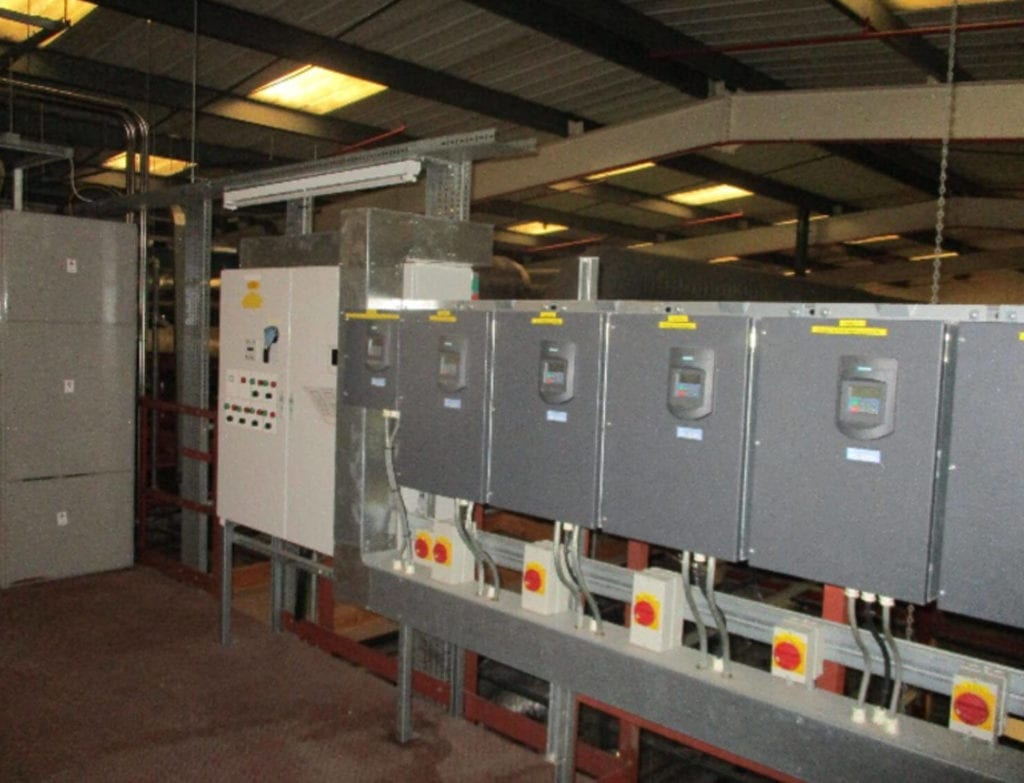
Special attention had to be given to the fire detection, alarm and sprinkler system, which had to be functional for the duration of the works and retained for future use. The intricate web of electrical services in the service area was fed from an adjacent plant room and each cable had to be traced, identified and either terminated or re-routed and replaced (if not compliant), by our in-house Electrical Engineer, prior to commencing the dismantling works. Close and regular liaison with client’s project manager ensured that any concerns were dealt with in a positive and informed manner.
Where practically possible all structures were reduced by a variety of machines ranging from small robotically operated equipment to a 7-tonne tracked 360⁰ demolition rig with attachments designed for specific demolition activities. Mobile elevated work platforms, fork lifts and skid steer loaders were utilised to access areas and to assist in the removal of all arisings. Air extraction systems and engineered dust control measures such as water sprays and other controls required for safety and health purposes substantially reduced diesel fume emissions and dust. Furthermore, where available, electrically operated machinery and electrical/ electronic equipment was utilised to minimise and control diesel fume emissions.
The reduction process was top-down, shearing away each structural element from the next. Sections were taken down a bay at a time. Each section of the structure was evaluated for its integrity and reliance on adjacent internal & external sections ensuring that stability of the structure was maintained until such time as the demolition process dictated otherwise. This process of reduction was repeated to all partition walling and columns as the demolition sequence progressed. No section was left unsupported or in a dangerous condition at any stage of the works. A banksman was additionally positioned strategically during these works to advice on any deviation in the vertical and perpendicular condition of the structure.
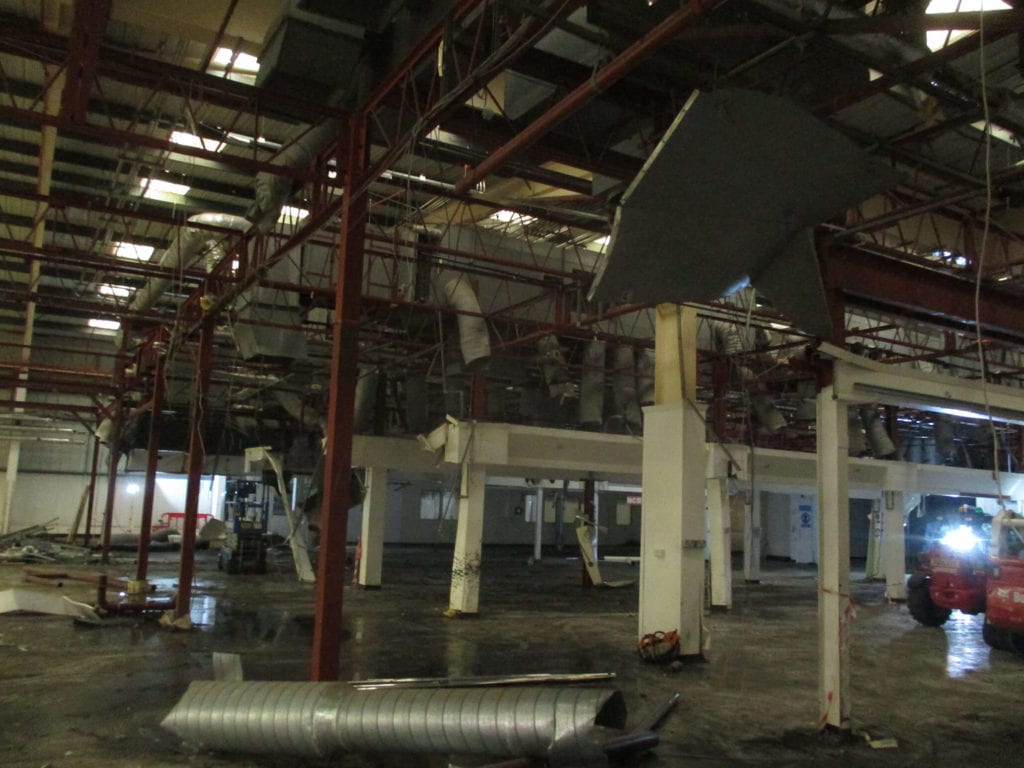
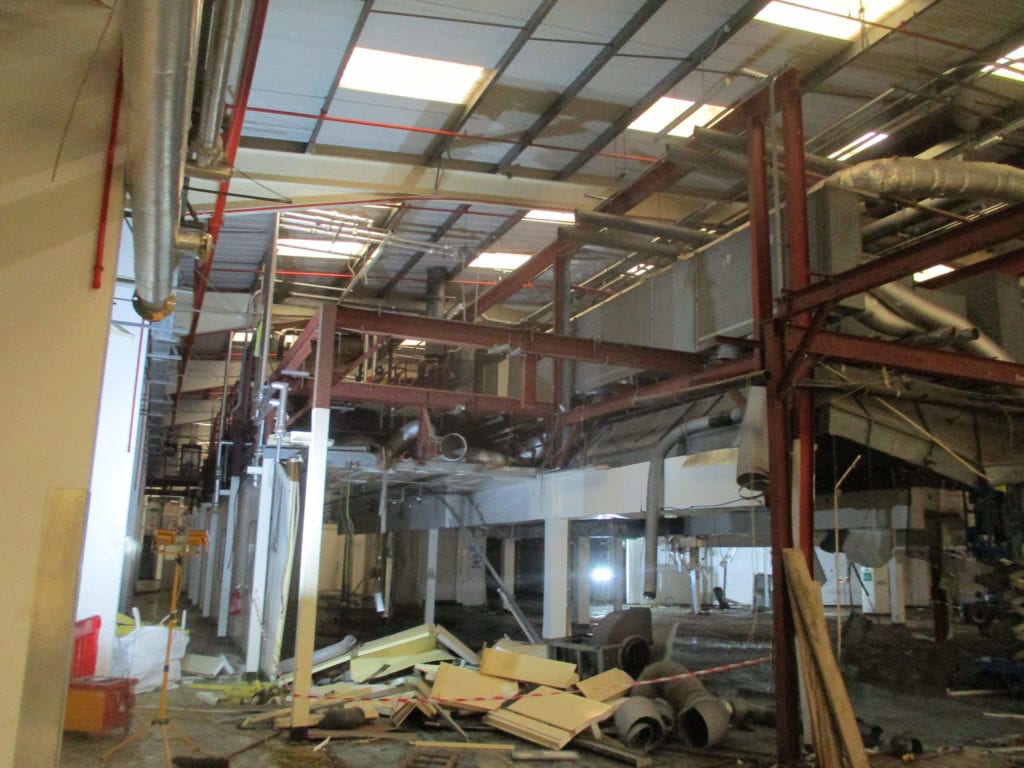
A major challenge was in removing demolition arisings through a narrow entrance/exit gate to the warehouse building. All material arisings had to be cut to suitable sizes insitu. Noise assessments were carried out as and when necessary. All operatives were aware of excessive noise levels, with recommended actions in place for operatives to adhere to at all times. Appropriate ear protection was worn as necessary and according to statutory controls.
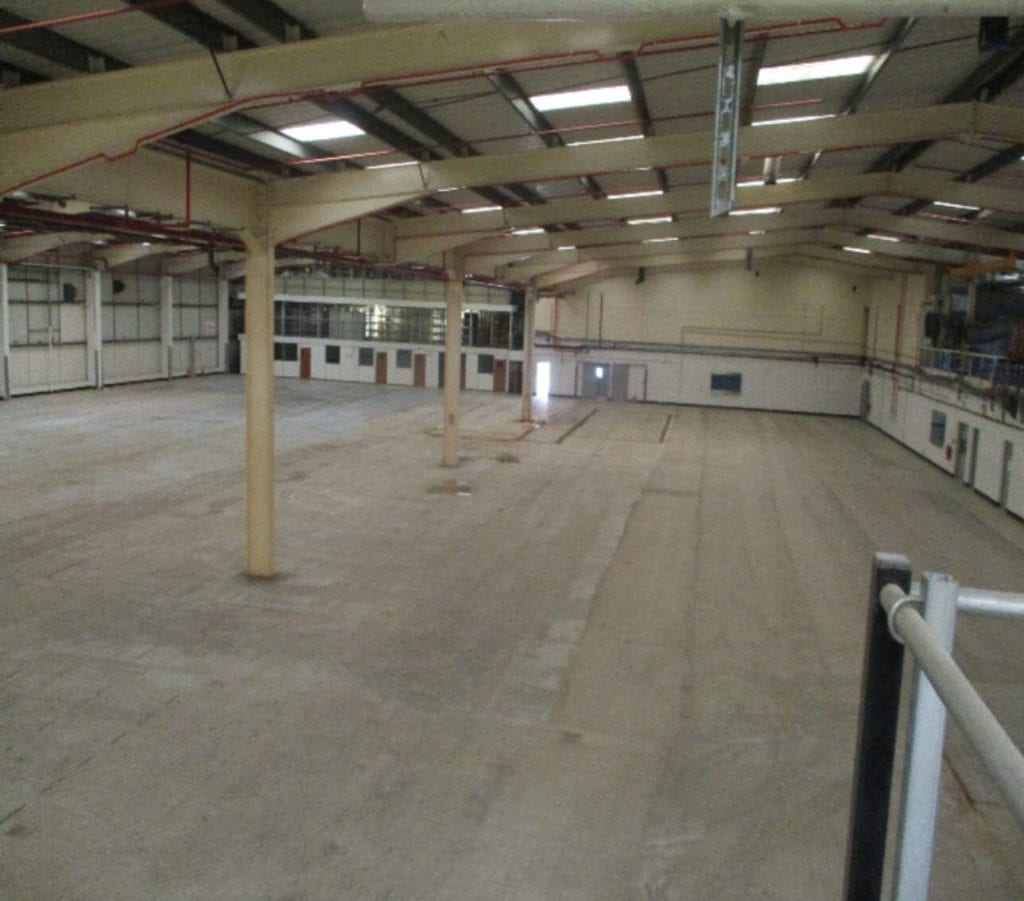
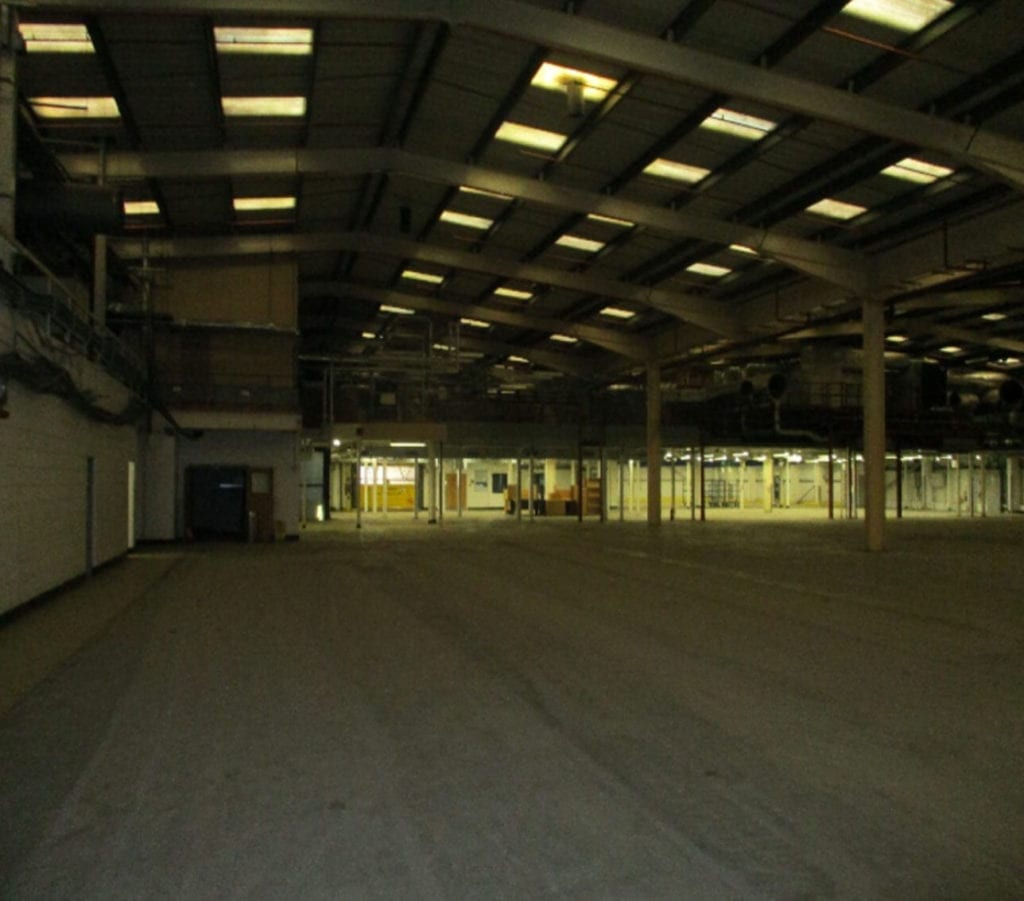
Dust levels were reduced to the minimum possible by careful and selective use of water sprays and other controls required for safety and health purposes.
As work progressed across the site the demolition material arisings were segregated and loaded away for recycling or disposal. In total, 44 tonnes of controlled waste were sent to a licensed waste transfer station, and 246 tonnes of steelwork were loaded away in roll on roll off bins to locally based metal recycling company.
Delivery of programmed works was well in advance of the agreed programme and enabled the building contractor an early start. The works were also completed within budget, with no incidents or accidents recorded.